World Day for Safety & Health at Work 2021
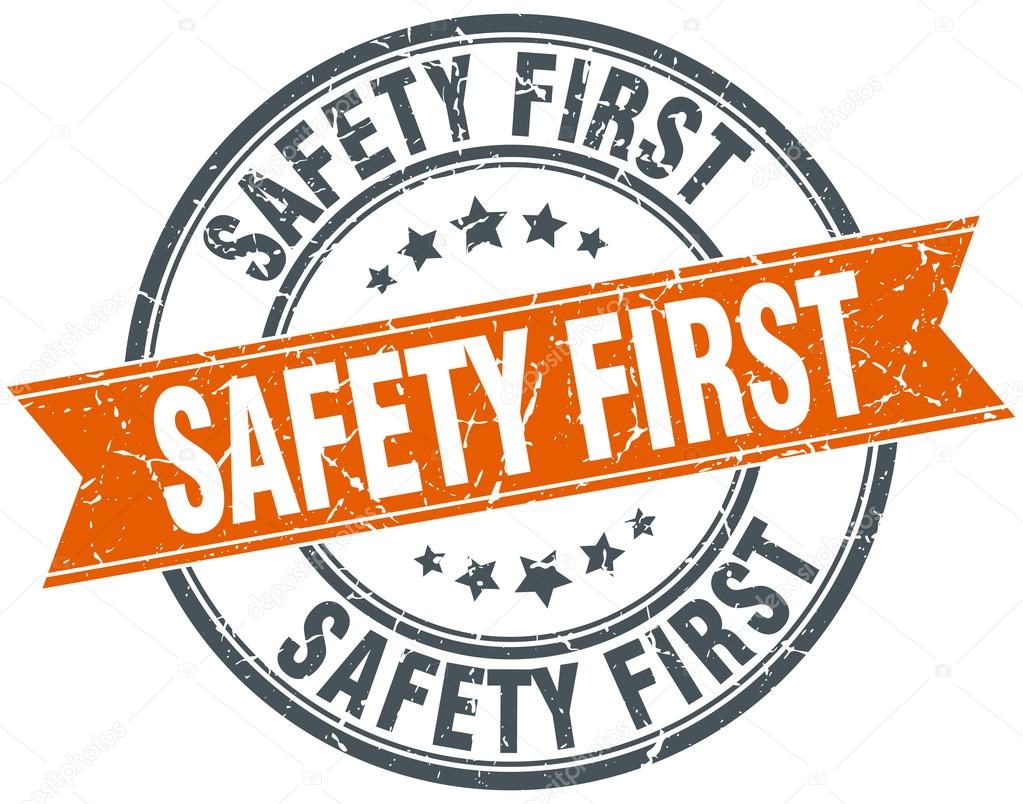
Every Day is World Day for Safety and Health at Work at Crown
The International Labour Organization (ILO) launched World Day for Safety and Health at Work in 2003 to raise awareness for the prevention of occupational accidents and diseases globally. As an international manufacturer that holds the health and wellbeing of its global associates in the highest regard, we are proud to support any campaign that promotes safe, healthy and decent work.
In this blog post, Laurent Leucio, Director, EHS Director, Sustainability and Excellence Projects, Crown Europe, highlights how employee engagement and investments in training have helped build a Total Safety Culture within Crown.
Q: What is Crown’s view on employee health and safety?
A: We believe that a safe and healthy workplace is a fundamental right of every person and a business imperative. It is built into every process, procedure and system of the Company as well as the attitudes and values of every employee – from top management down. And as technology has advanced, so too has the way we leverage it to ensure our employees are as safe and well as possible both in and out of the workplace.
We have been standardizing the data and information we collect across our global operations and have implemented state-of-the-art software to enable us to extrapolate, analyze and importantly, to act to make continuous improvements to the health and safety of our teams. We began from the ground up to ensure alignment from the outset and that we can create benchmarks based on accurate data.
Q: Tell us more about the way this data is being collected, why it is important and how it is used.
A: Everything relating to Environment, Health and Safety (EHS) is recorded – from incidents, audits and initiatives to inspections and safety cards – and those responsible at the plant level can enter information in real time via their smartphones. This allows them to undertake live inspections and record data instantly, instead of having to process the information when they get back to their desks. It is an immersive approach that our team has fully embraced. The software is currently in use in 60 locations across Europe, as well as in all other Crown plants globally. With this kind of overview, we can identify areas for improvement, whether there is a need for further training or support, or if there are issues that we believe training can mitigate future risk of incidents. However, we do not rely on measurement alone. Within each measurable parameter in our reporting there are mandatory training sessions that vary by region along with modules that are requirements for every associate around the world.
Q: What other health and safety initiatives are in place across the Company?
A: Behavioral safety is a primary focus of our Total Safety Culture philosophy, along with governmental compliance and auditing. This has taken shape through several initiatives.
The SAFE program involves many thousands of observations each year by peers to foster increased safety dialogue and to identify safer working methods. This program has proven to be effective in reducing incidents and injuries by increasing the visibility of unsafe behaviors through skill development, providing total employee participation and instilling safety as a “core Crown value.” As employees develop their observation and communication skills, their communication comfort level increases in the process and safety coaching becomes an integral part of the work culture.
Our Safety Circles program creates an opportunity for employees to take ownership of safety, both for themselves and others. The “circles” involve groups of four to five employees from several departments or areas. They discuss ways to improve safety and provide feedback to plant management quarterly. Many excellent ideas have emerged from this dialogue, strengthening our safety program.
In Europe, our Human Factor Training enables employees to examine how their behaviors can impact their personal safety and those around them. Delivered to groups of 20 employees at a time, the program asks individuals to assess and identify themselves as one of four possible safety categories based upon their behavioral state at a given point in time. Once this assessment has been completed, they investigate ways of modifying their behavior to become a safer person both at work and at home.
Outside of these formal programs, we run activities around topics like nutrition and exercise. They can be as simple as having a fruit day at work or organizing bicycle rides or football matches on the weekends. These soft initiatives are important as they encourage and support the healthy mindset and behavior and increase the engagement levels of our teams.
Q: How else is Crown’s Total Safety Culture reinforced?
A: Management engagement is prioritized across our global operations. Our EHS managers are in continuous contact with their team members on the factory floor. These discussions form the building blocks of a dialogue related to EHS and are invaluable as those working on the lines will share recommendations for improvements that we may not have thought about otherwise. It creates a critical learning opportunity for us and allows us to take corrective action as needed.
To facilitate employee access to safety training and maintain an open dialogue with EHS experts in our plants, we have implemented a modern Learning Management System (LMS). The system delivers training in 15 language on a variety of safety topics using videos, quizzes and other formats. Topics are selected based on our safety statistics and are designed to help employees better understand their work environment and make our workplace even safer.